Red Wing Made - Assembly
Red Wing boots are put together with traditional construction techniques that transform premium materials into supremely durable boots and shoes. It takes skilled craftsmanship and expertise of the assembly process to achieve such consistently superior quality. While technology has improved over time, the techniques and skills it takes to build our boots still pulls strongly from the past.
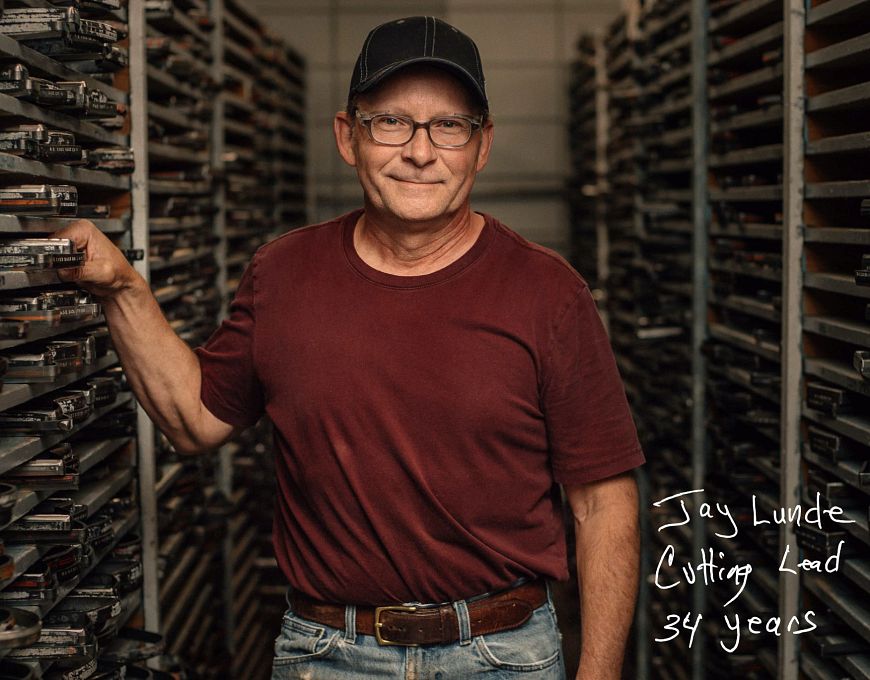
CUTTING
The shoemaking process begins with cutting the leather for the shoe. The quick, precise movements of the cutter reflect years of experience. Every bit of leather gets used. There are no unnecessary motions.
Jay Lunde is a highly trained leather cutter with hands-on expertise earned over a 34-year career. Jay and his peers have an uncanny ability to read each piece of leather for parts of each piece that can be cut and used for the best performance in different parts of every boot.
Today we cut leather in two ways, depending on the job: by hand with a hand press — a craft that dates back to the 1800s — and with an advanced, highly efficient laser-cutting machine. Jay is one of only a few individuals in the whole plant who can still use a hand press with ease. He followed in the footsteps of his father, who worked 40 years in the Red Wing factory.
The shoemaking process begins with cutting the leather for the shoe. The quick, precise movements of the cutter reflect years of experience. Every bit of leather gets used. There are no unnecessary motions.
Jay Lunde is a highly trained leather cutter with hands-on expertise earned over a 34-year career. Jay and his peers have an uncanny ability to read each piece of leather for parts of each piece that can be cut and used for the best performance in different parts of every boot.
Today we cut leather in two ways, depending on the job: by hand with a hand press — a craft that dates back to the 1800s — and with an advanced, highly efficient laser-cutting machine. Jay is one of only a few individuals in the whole plant who can still use a hand press with ease. He followed in the footsteps of his father, who worked 40 years in the Red Wing factory.
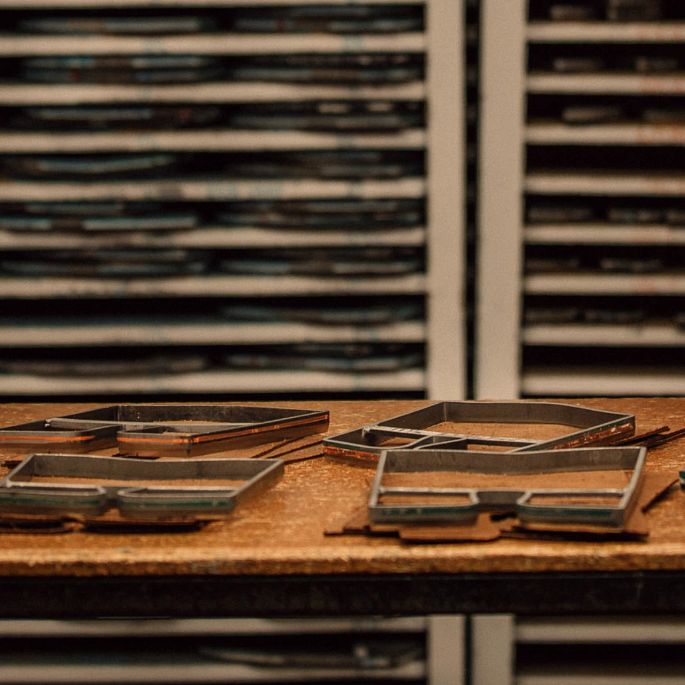
CUTTING
The shoemaking process begins with cutting the leather for the shoe. The quick, precise movements of the cutter reflect years of experience. Every bit of leather gets used. There are no unnecessary motions.
Jay Lunde is a highly trained leather cutter with hands-on expertise earned over a 34-year career. Jay and his peers have an uncanny ability to read each piece of leather for parts of each piece that can be cut and used for the best performance in different parts of every boot.
Today we cut leather in two ways, depending on the job: by hand with a hand press — a craft that dates back to the 1800s — and with an advanced, highly efficient laser-cutting machine. Jay is one of one of only individuals in the whole plant who can still use a hand press with ease. He followed in the footsteps of his father, who worked 40 years in the Red Wing factory.
The shoemaking process begins with cutting the leather for the shoe. The quick, precise movements of the cutter reflect years of experience. Every bit of leather gets used. There are no unnecessary motions.
Jay Lunde is a highly trained leather cutter with hands-on expertise earned over a 34-year career. Jay and his peers have an uncanny ability to read each piece of leather for parts of each piece that can be cut and used for the best performance in different parts of every boot.
Today we cut leather in two ways, depending on the job: by hand with a hand press — a craft that dates back to the 1800s — and with an advanced, highly efficient laser-cutting machine. Jay is one of one of only individuals in the whole plant who can still use a hand press with ease. He followed in the footsteps of his father, who worked 40 years in the Red Wing factory.
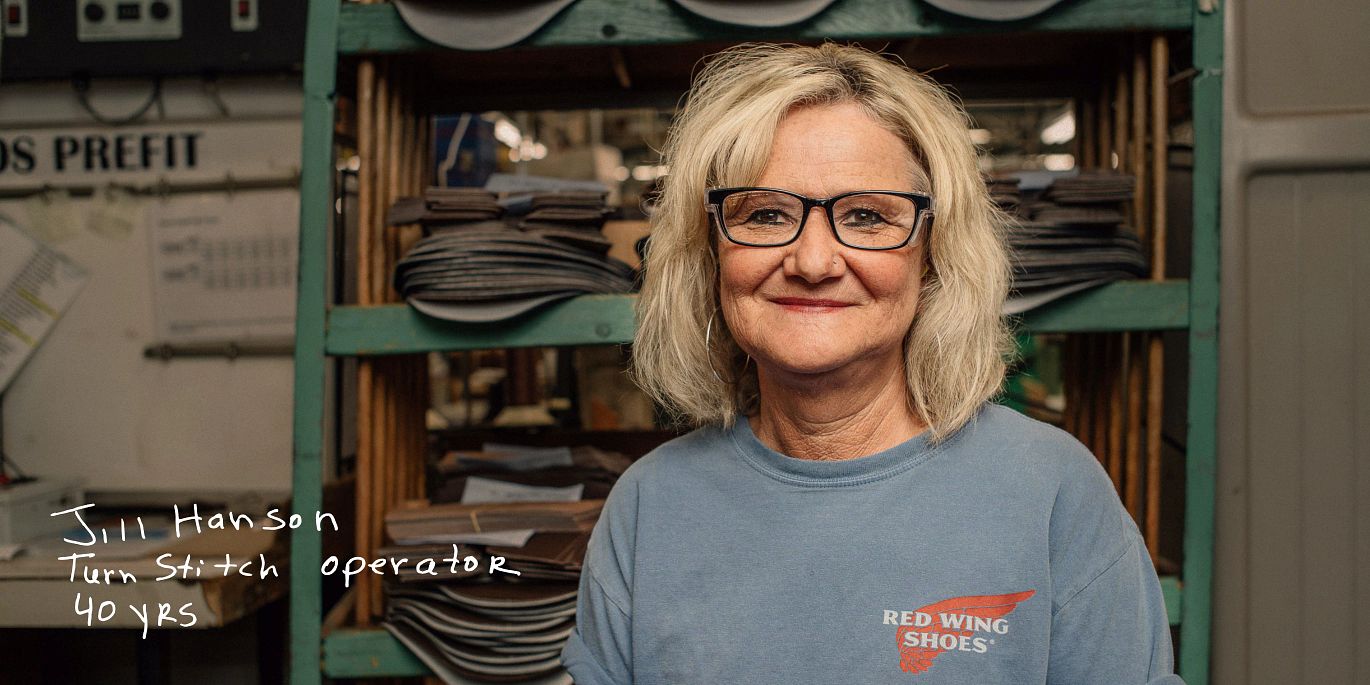
FITTING
Here is where the leather starts looking like a boot, as cut pieces are meticulously stitched together by seasoned sewing experts to form the footwear upper. Many of these operators work on the same century-old Puritan sewing machines that were used in the earliest years of the Red Wing Shoe Company.
Jill Hanson is a 40-year employee of Red Wing Shoes who was hired by Bill Sweasy, Jr., and started her career turn stitching — a technique that involves finishing seams or edges for a clean, flat finish. After performing a variety of roles over the years, she is back to turn stitching once again.
Jill has witnessed many exciting changes over her tenure at Red Wing, but one thing has been constant is the community she has found at the company. With many of her family members working alongside her, she has never felt a shortage of support.
Here is where the leather starts looking like a boot, as cut pieces are meticulously stitched together by seasoned sewing experts to form the footwear upper. Many of these operators work on the same century-old Puritan sewing machines that were used in the earliest years of the Red Wing Shoe Company.
Jill Hanson is a 40-year employee of Red Wing Shoes who was hired by Bill Sweasy, Jr., and started her career turn stitching — a technique that involves finishing seams or edges for a clean, flat finish. After performing a variety of roles over the years, she is back to turn stitching once again.
Jill has witnessed many exciting changes over her tenure at Red Wing, but one thing has been constant is the community she has found at the company. With many of her family members working alongside her, she has never felt a shortage of support.

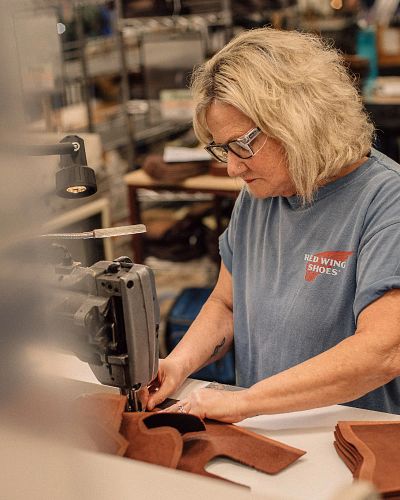
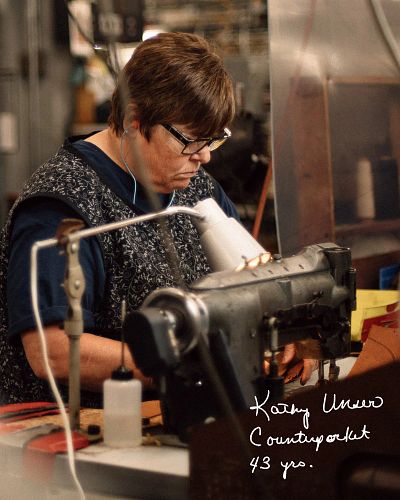
"Everything is so handcrafted. You have to really have a talent to do it and catch on. We travel around a lot on our motorcycle and people see us wearing Red Wing Boots, and they're so impressed that I can make that boot."
-JILL HANSON
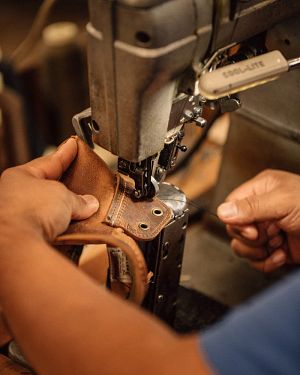
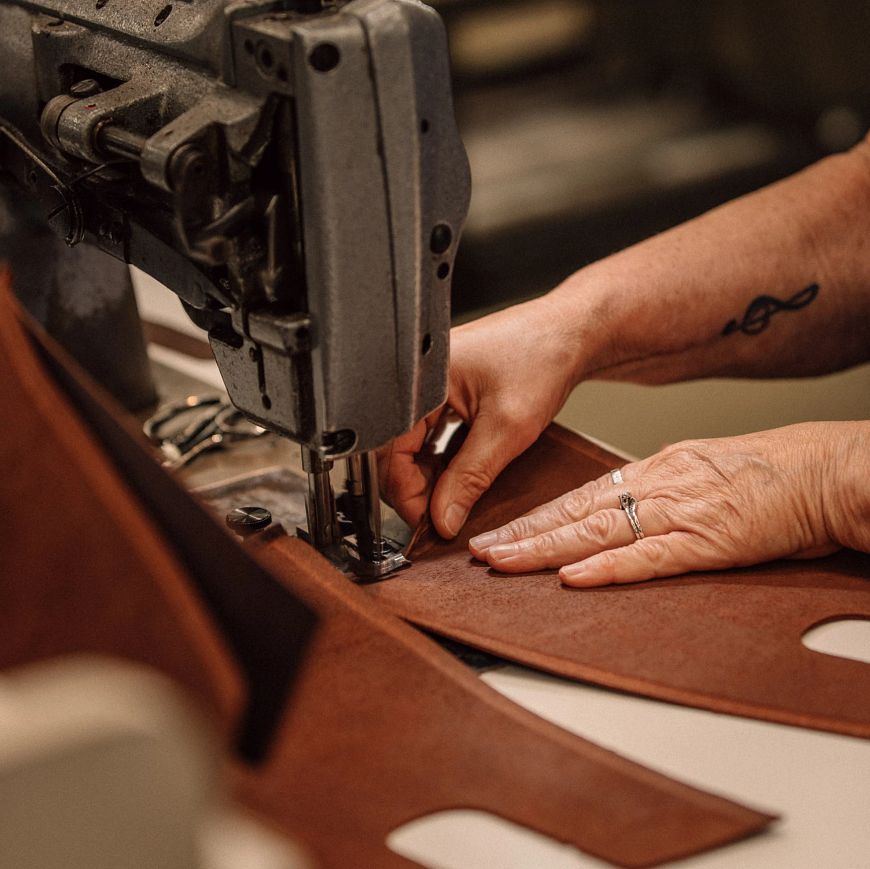
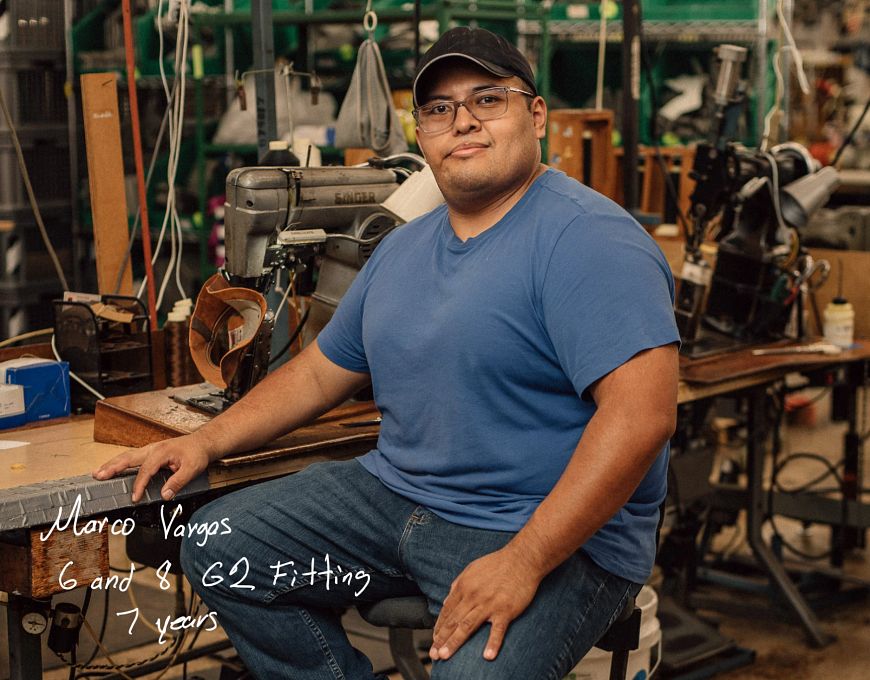
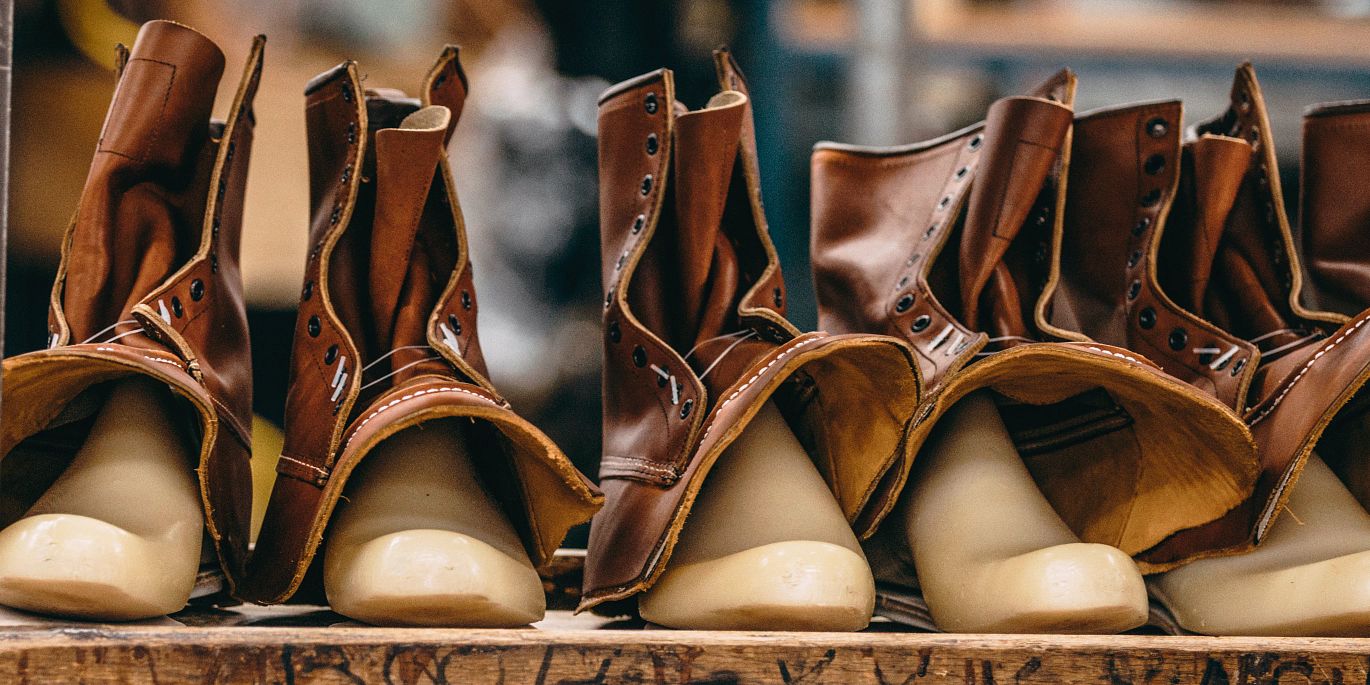
LASTING
To precisely form the shape of our footwear, the leather is pulled over a foot-shaped object called a last. The shape of the last varies depending on footwear style. Once the leather is secured over the last, the shoe is welted or stitched down, depending on construction.
To precisely form the shape of our footwear, the leather is pulled over a foot-shaped object called a last. The shape of the last varies depending on footwear style. Once the leather is secured over the last, the shoe is welted or stitched down, depending on construction.
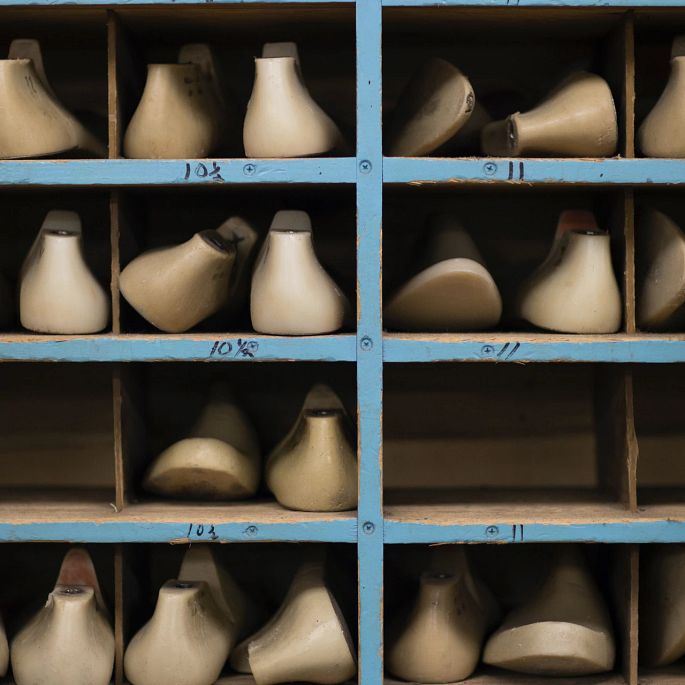
LASTING
To precisely form the shape of our footwear, the leather is pulled over a foot-shaped object called a last. The shape of the last varies depending on footwear style. Once the leather is secured over the last, the shoe is welted or stitched down, depending on construction.
To precisely form the shape of our footwear, the leather is pulled over a foot-shaped object called a last. The shape of the last varies depending on footwear style. Once the leather is secured over the last, the shoe is welted or stitched down, depending on construction.
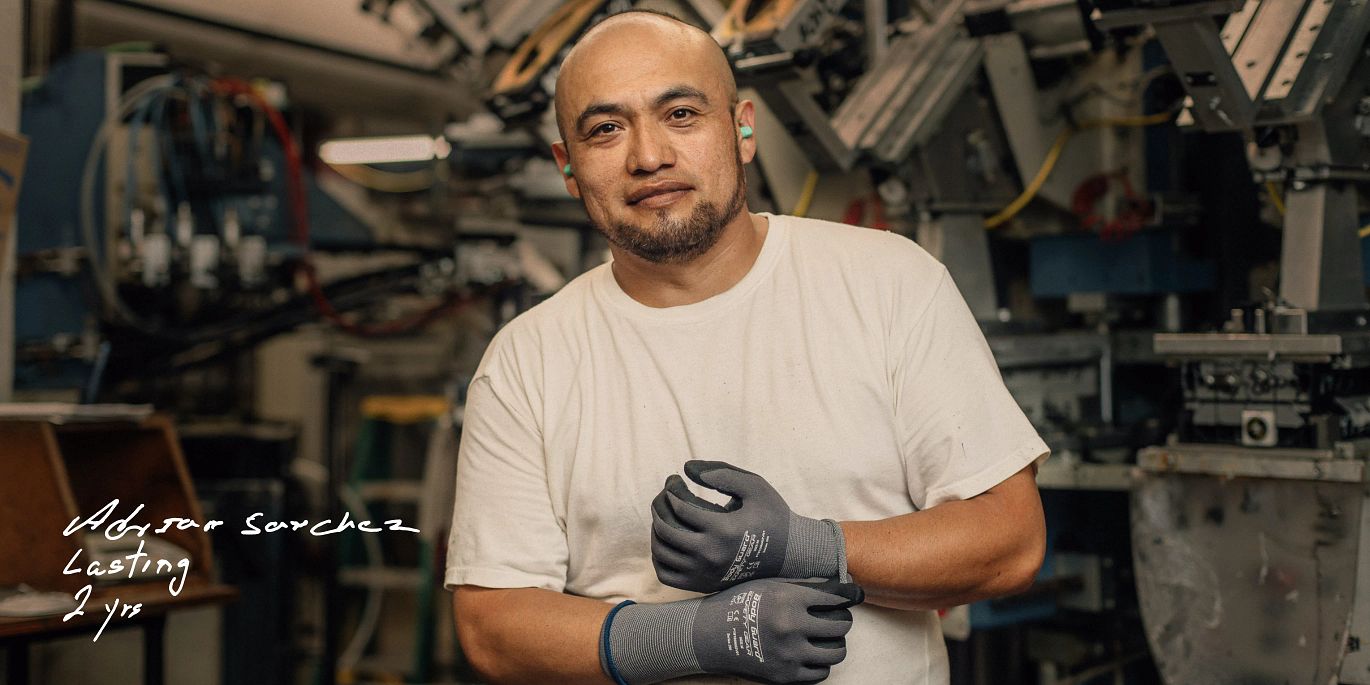
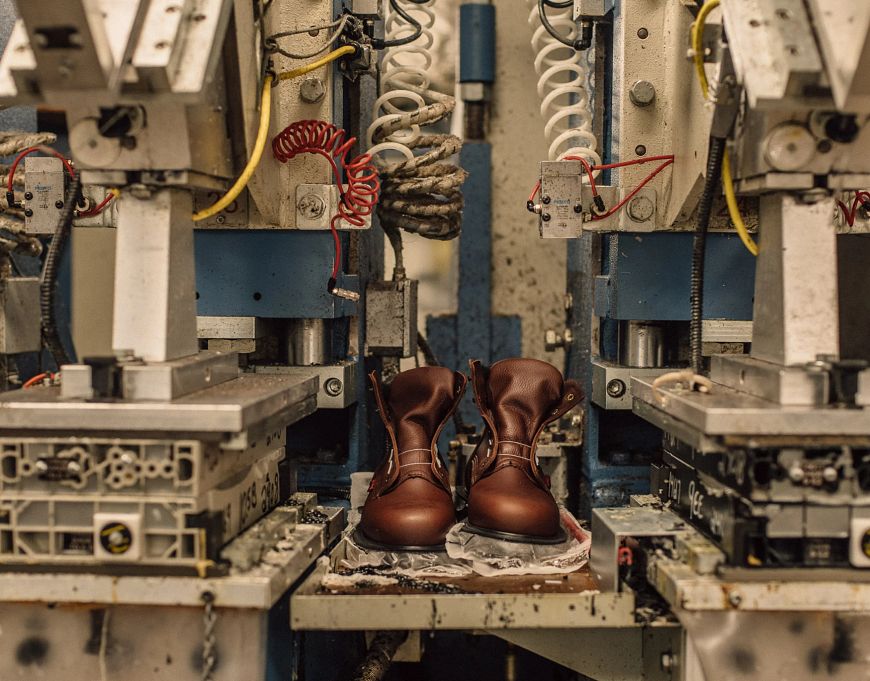
WELTING + BOTTOMING
After lasting is complete, the outsole gets manually stitched or glued to the midsole. This is a crucial step in the boot-making process – one that requires excellent hand/eye coordination to ensure that the final step in the construction process is performed perfectly. Red Wing uses several different types of soles, each with a specific tread pattern, shape and composition.
Adrian Sanchez Figuera has been with Red Wing for 2 years, performing a variety of roles within the plant. His relentless desire to learn and master new skills pushed him to spend three weeks focused specifically on perfecting the bottoming process.
After lasting is complete, the outsole gets manually stitched or glued to the midsole. This is a crucial step in the boot-making process – one that requires excellent hand/eye coordination to ensure that the final step in the construction process is performed perfectly. Red Wing uses several different types of soles, each with a specific tread pattern, shape and composition.
Adrian Sanchez Figuera has been with Red Wing for 2 years, performing a variety of roles within the plant. His relentless desire to learn and master new skills pushed him to spend three weeks focused specifically on perfecting the bottoming process.
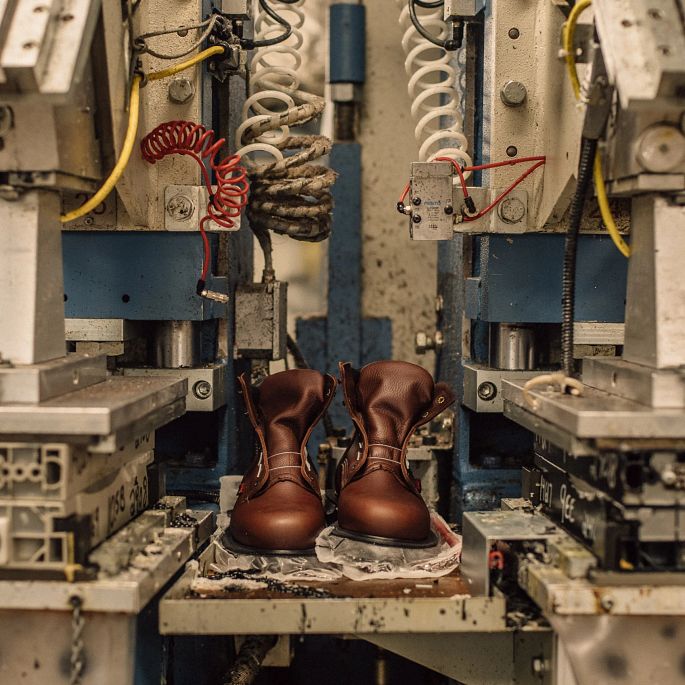
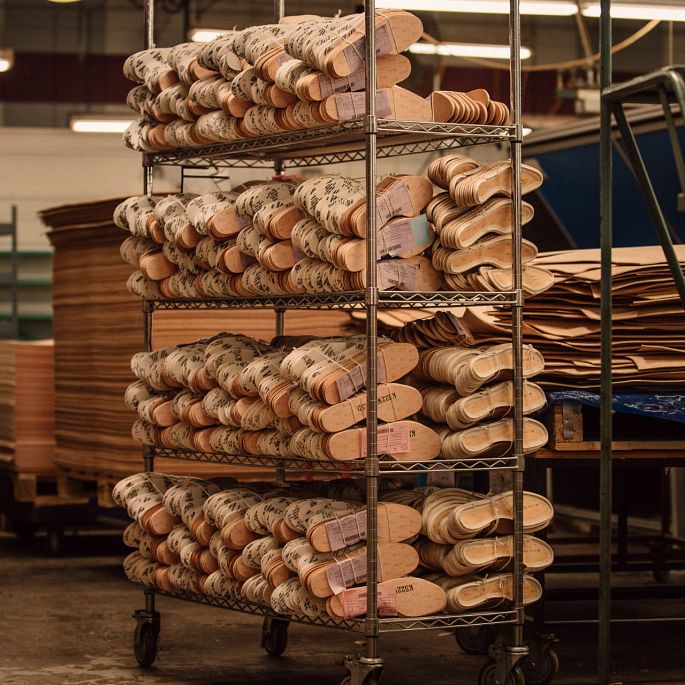
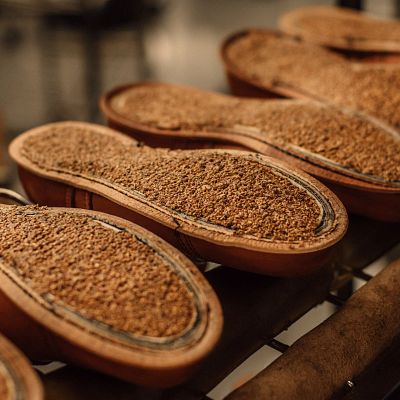
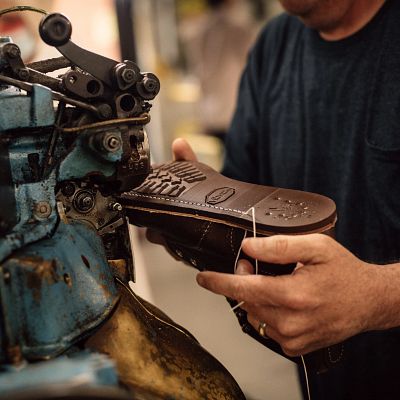
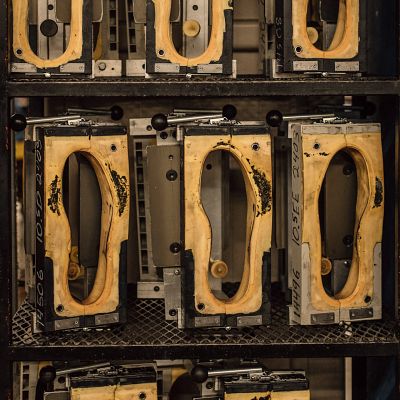
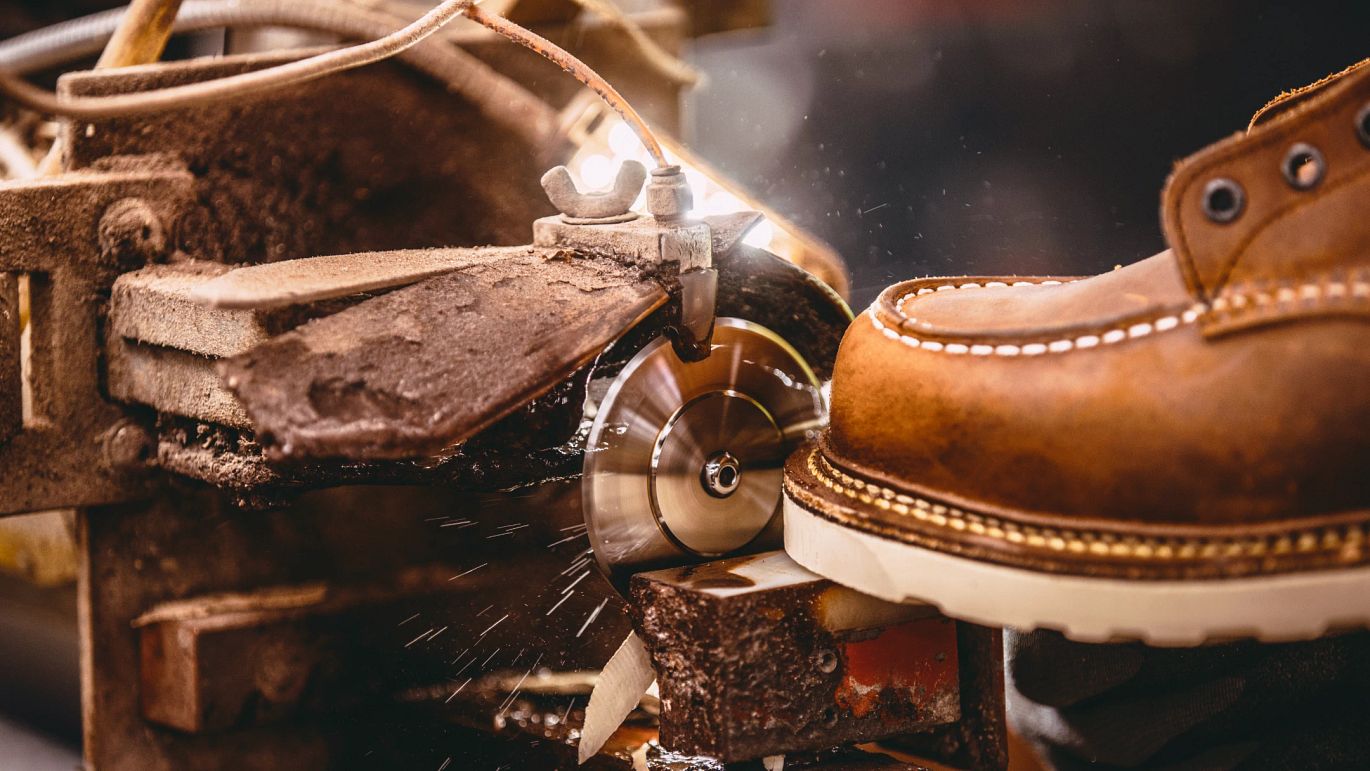
FINISHING
Carefully inspect every boot once — and then start over and do the whole thing again. This is what happens to every pair of boots before they go into the box. Those that pass the test get cleaned, polished and brushed before they're packaged up.
Carefully inspect every boot once — and then start over and do the whole thing again. This is what happens to every pair of boots before they go into the box. Those that pass the test get cleaned, polished and brushed before they're packaged up.
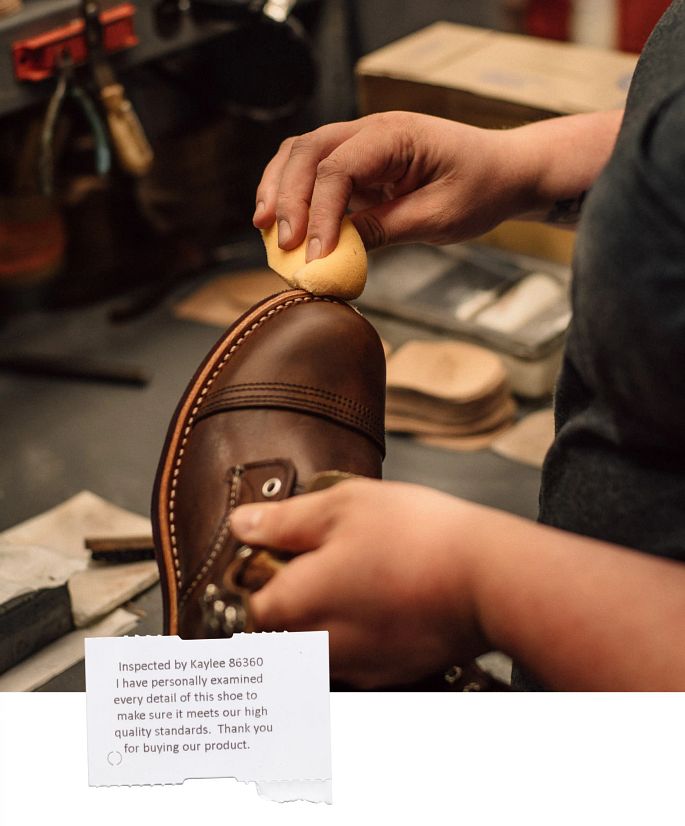
FINISHING
Carefully inspect every boot once — and then start over and do the whole thing again. This is what happens to every pair of boots before they go into the box. Those that pass the test get cleaned, polished and brushed before they're packaged up.
Carefully inspect every boot once — and then start over and do the whole thing again. This is what happens to every pair of boots before they go into the box. Those that pass the test get cleaned, polished and brushed before they're packaged up.